Tiger Motors
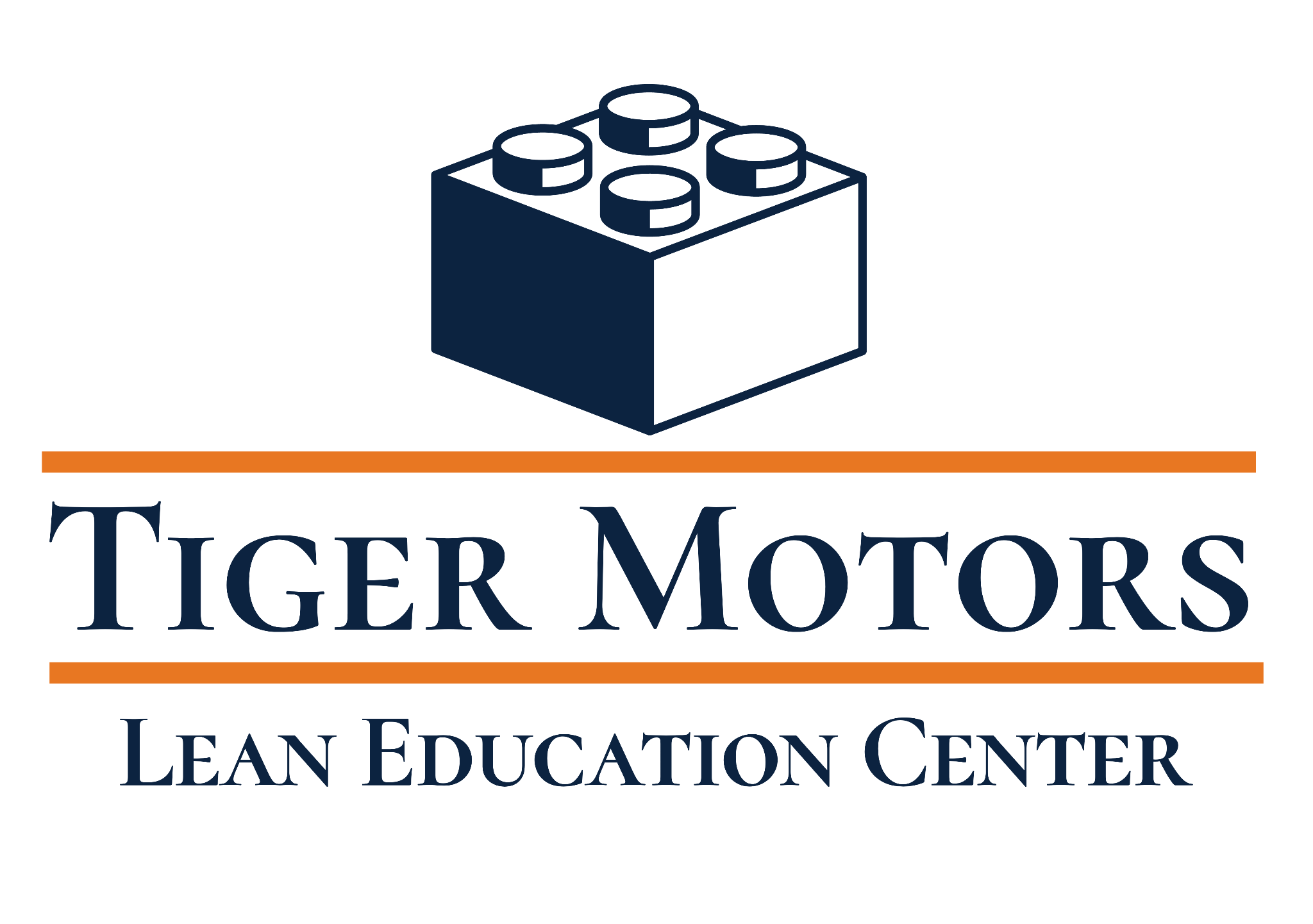
HISTORY OF THE LAB
The initial project was established in 2011 to allow us to bring lectures to life and use a hands-on, experiential learning approach to best manufacturing practices by emulating a high-volume auto plant. It allows us to build a product from start to finish, showing how various systems interact.
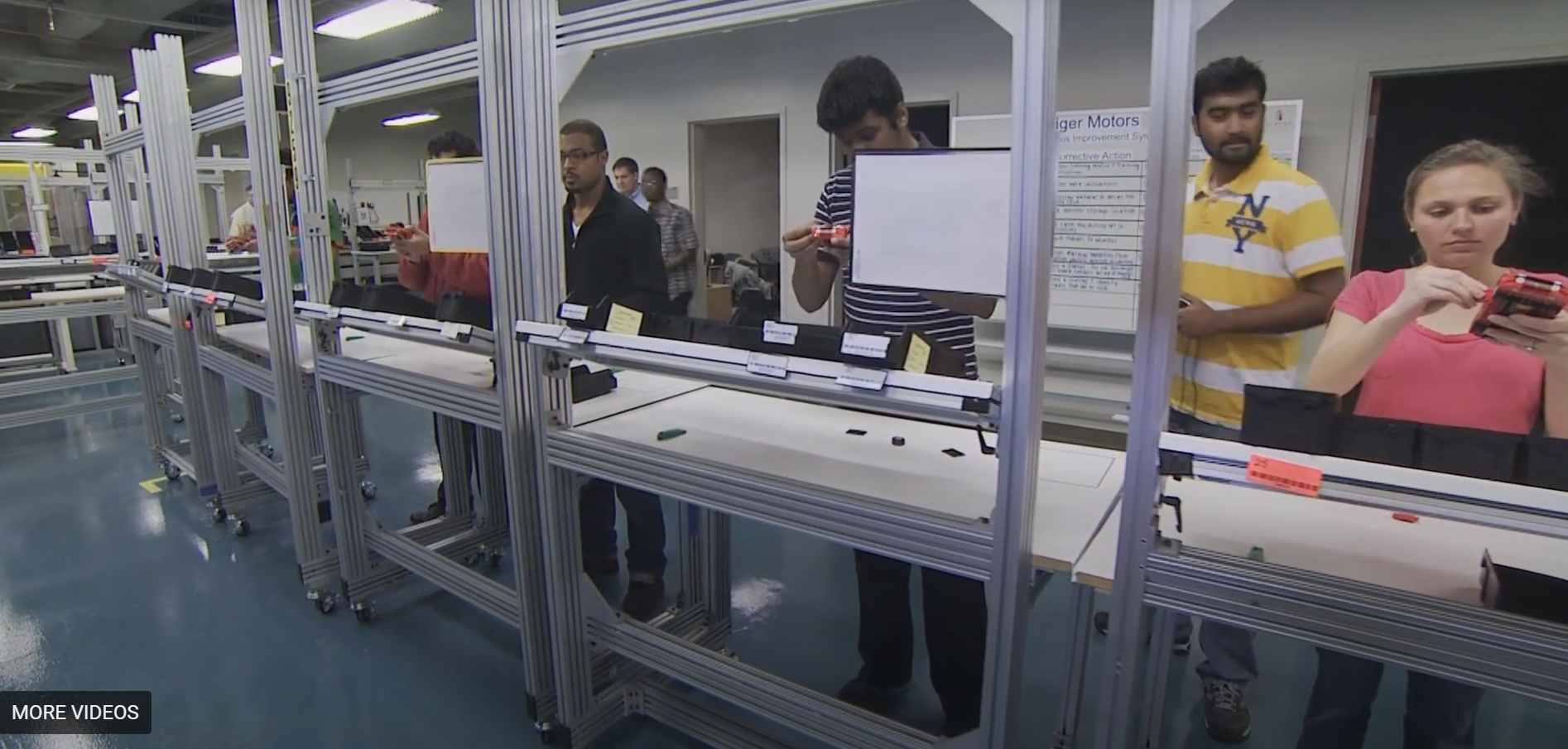
LOCATION & PURPOSE
The lean education center is located in our 4,000-square foot lab facility in the Samuel Ginn College of Engineering at Auburn University and allows students to transform a complex manufacturing environment from mass production to a lean production system all at the hands of our students.
Learning the concepts in a lecture or through a video doesn’t solidify an understanding the way the activities in the lab can. Lean is a culture and a way of thinking. Without feeling the pressure to overproduce and seeing for yourself the effect of one’s natural tendencies to hoard parts and work ahead a manager will never fully grasp the value of single piece flow and the importance of standardization. Â
Our vision is to provide students a path to understand the value of Lean for themselves. The lab, with the approximately 250-piece LEGO vehicles that are simple to learn, puts a sense of fun into the activity and breaks down barriers towards experiencing the culture of Lean. Another aspect of Tiger Motors is the opportunity for students to experience state-of-the-art technology that can aid in-station inspection, provide training, and demonstrate automated end-of-line quality check.Â
Director, Tom Devall, is often quoted saying that the students in the lab have an equivalent of 10 years Lean experience when they complete their term of a couple years. This is similar to learning a foreign language through immersion.Â
WHERE WE ARE TODAY
The assembly line at Tiger Motors simulates the processes of the Toyota Production System using part quantities and cycle times similar to what is found in the automotive industry.Â
Students build two different types of vehicles, a 277-piece sports car, and a 234-piece SUV, in 60-second cycles.Â
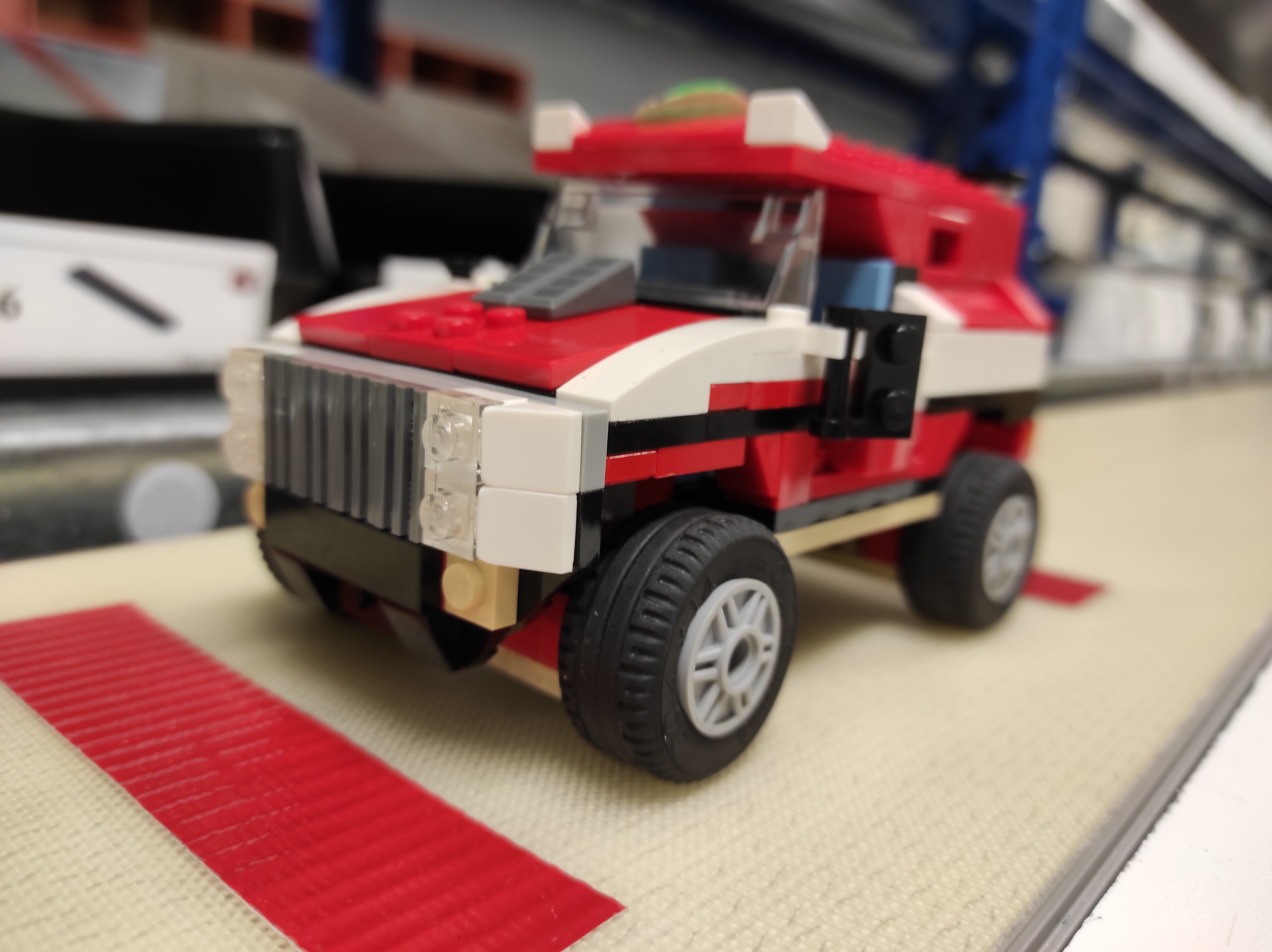
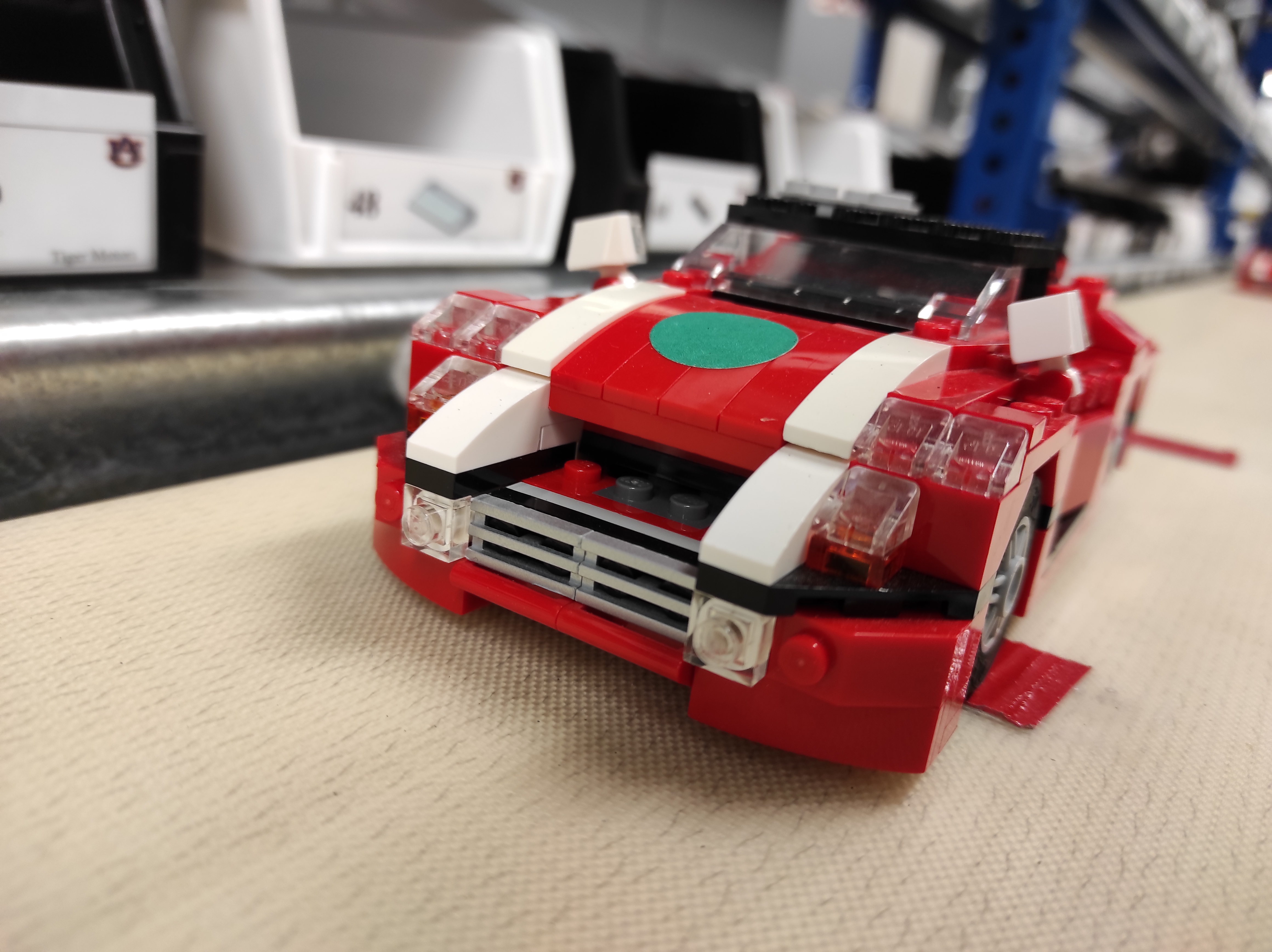
The lab can accommodate up to 25 students at a time at 15 workstations. Engineering students work in the lab several times during each semester and allows them to witness the dramatic transformations that occur during the manufacturing process.Â
LEGO® blocks are used because they are excellent for simulating real-world manufacturing processes, inventory issues, overproduction runs, defects, and quality problems. For instance, when working with tiny blocks at high speeds, it is easy to misplace a part and not know it.
LAB FEATURES